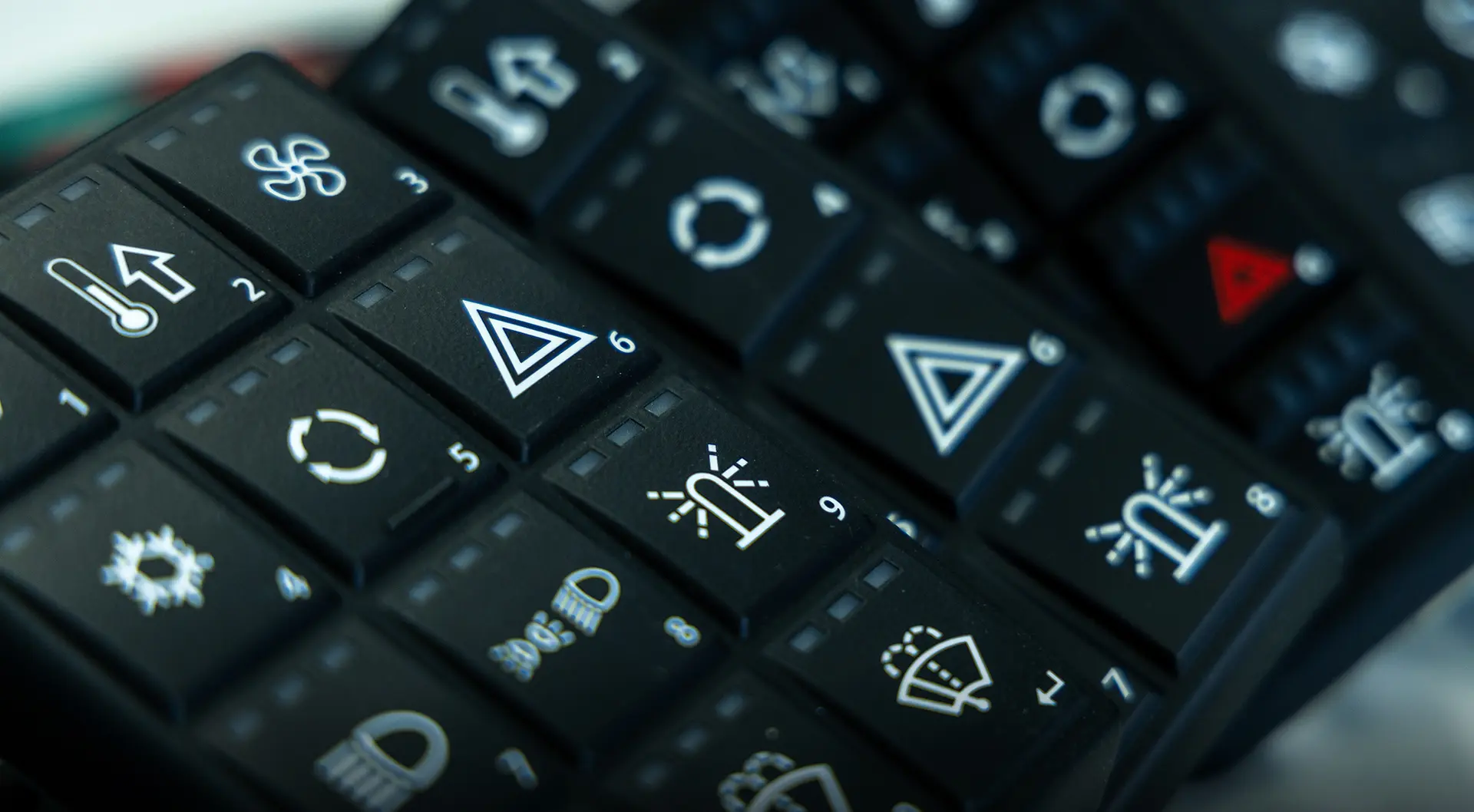
In the complex symphony of a modern vehicle, numerous vital electronic actors play their parts. From brakes harmonizing with engine management to safety equipment providing a crescendo, their seamless communication is paramount. Enter the CAN bus system, the conductor orchestrating this intricate performance.
For makers of vehicle controls, the CAN bus isn't just a stage; it's a problem-solving toolbox. What problems does this ubiquitous system tackle, and how can savvy control makers leverage its power to create better, safer, and more efficient vehicles?
CAN Bus Untangled: Reduced Complexity and Weight
Imagine a sprawling metropolis served by a spaghetti junction of roads. That's what vehicle wiring resembled before the CAN bus system. Dedicated wires for each function tangled the chassis, adding weight, complexity, and susceptibility to faults. The CAN bus, with its single twisted-pair cable, slashed this Gordian knot.
Devices, or nodes, on the network "talk" using message-based communication, eliminating the need for point-to-point wiring. This translates to lighter vehicles, less fuel consumption, and a cleaner, more manageable layout. For control makers, it means smaller footprints for their interfaces, easier installation, and the freedom to focus on functionality rather than wiring acrobatics.
Enhanced Data Sharing and Analysis
The CAN bus doesn't just streamline communication; it democratizes it. Every node, from engine control units to your custom display, can access and contribute data across the network. This real-time information exchange empowers advanced functionalities. Imagine a keypad sending engine temperature data to a display or a vehicle interface controller receiving speed and fuel level inputs to optimize performance.
This data symphony benefits control makers in several ways. First, it opens doors to innovative features and user experiences. Imagine a keypad displaying dynamic shift points based on engine load or a climate control system adjusting based on real-time fuel efficiency data.
Second, diagnostic capabilities are enhanced. Faults can be pinpointed quickly and accurately, aiding in quicker repairs and improved maintenance schedules.
Robustness and Fault Tolerance
Vehicles operate in harsh environments, enduring everything from scorching sun to bone-chilling frost.
The CAN bus system is built to weather these storms. Its differential signal transmission minimizes electrical noise, while its message-based protocol incorporates error-checking and collision avoidance mechanisms. Even if a node malfunctions, the network stays resilient, preventing cascading failures.
For control makers, this translates to dependable products. Their displays won't flicker due to electrical gremlins, and their keypads won't become unresponsive in extreme temperatures. This builds trust with both vehicle makers and end users, leading to a stronger market position.
Customization Concerto: Adaptability and Scalability
This system isn't a one-size-fits-all solution. Its modularity allows for customization and scalability, catering to diverse vehicle types and control needs. Different message priorities can be assigned, ensuring critical information delivery even in congested networks. Additionally, various CAN transceivers and physical layers support different data rates and cable lengths, adapting to various vehicle sizes and complexities.
This flexibility empowers control makers to develop solutions for a wider range of applications. A single keypad design can be adapted to different dashboards. At the same time, a vehicle interface controller can be scaled to handle the communication needs no matter the size of the vehicle.
Beyond the Vehicle: Broader Applicability and Future Potential
The CAN bus system’s problem-solving prowess extends to agricultural machinery, marine vessels, construction equipment, and even medical devices. The ability to share data reliably and efficiently makes it a valuable tool in any system where interconnected components need to work in harmony.
As technology evolves, it continues to adapt. New versions support higher data rates, increased security, and integration with other communication protocols. This opens doors for even more complex and innovative control systems in the future.
Problem Solver to Partner: Empowering Control Makers
For makers of vehicle controls, the system isn't just a technology; it's an innovation partner.
By understanding its strengths and capabilities, control makers can unlock a world of possibilities, creating solutions that are lighter, smarter, more reliable, and adaptable. So, embrace the symphony of these systems. and let its problem-solving power harmonize with your own to craft the future of vehicle control.
This is just the beginning of these systems and stories. As technology advances and control systems become even more sophisticated, it will undoubtedly continue to evolve, providing a robust and adaptable platform for makers to build upon. The future of vehicle control is collaborative, and it is the conductor ensuring all the instruments play in perfect harmony.
The Future of the Can Bus
For decades, the Controller Area Network (CAN bus) has served as the unsung hero of the vehicle industry, silently orchestrating the complex symphony of onboard electronics. Ensuring smooth engine communication, it's the invisible conductor keeping vehicles humming.
But the CAN bus system, like the vehicles it governs, is not immune to the winds of change. As technology gallops forward, the future for vehicle makers unfolds, painted with both challenges and dazzling possibilities.
Ultimately, the future of these systems isn't a question of "if" but "how." By understanding its potential, leveraging its strengths, and adapting to the changing technological landscape, vehicle makers can unlock a world of safer, smarter, and more connected vehicles.
This symphony may evolve, but its melody of efficiency and reliability will continue to resonate for years to come, ensuring the smooth ride of the vehicle industry on the road to the future.
Precision And Harmony
Precision will be the conductor of this technological orchestra, ensuring every instrument – sensor, ECU, display – plays in perfect harmony. But this harmony relies on a vital element: precision. Just like a slightly off-key note can mar the performance, inconsistencies in the system can lead to functional hiccups, data errors, and even safety hazards. So, what does precision entail in these particular worlds? It encompasses several key areas:
- Timing: Messages on the network must arrive exactly when expected, measured in microseconds. Delays or jitter can disrupt communication and lead to missed commands.
- Signal Integrity: Electrical noise and interference can distort the data stream, causing misinterpretations. Precise signal conditioning and routing ensure messages remain crisp and clear.
- Data Accuracy: Every bit of information transmitted must be error-free. Robust error-checking mechanisms and redundancy measures guarantee data integrity.
- Synchronization: All nodes on the network must operate on the same beat. Precise synchronization ensures smooth communication and prevents conflicting messages.
Achieving this level of precision requires meticulous attention to detail throughout the design and implementation process. From choosing the right components and cables to employing best practices in layout and shielding, every step matters.
The rewards, however, are significant. A precisely crafted CAN bus system delivers reliable, consistent communication, enabling advanced features, enhancing safety, and ultimately, contributing to smoother, more enjoyable experiences.
In short, precision in the system’s design and implementation is paramount, impacting data accuracy, timing, signal integrity, and synchronization.
Embracing the Future: Opportunities
For vehicle makers, navigating this evolutionary landscape presents both challenges and exciting opportunities. Here are some key strategies to thrive in the future of the CAN bus system:
- Invest in Expertise: Building internal expertise in such technologies, both present and future, is crucial. This includes understanding new protocols, embracing software-defined networks, and staying abreast of security best practices.
- Partner with Experts: Collaborate with established solution providers and technology leaders. Leverage their expertise to design, implement, and maintain robust and future-proof network architectures.
- Embrace Flexibility: Adopt modular and adaptable system designs. Be prepared to integrate new protocols and technologies alongside the existing infrastructure without sacrificing efficiency or performance.
- Prioritize Security: Make cybersecurity a top priority. Implement robust security measures throughout the network to protect against cyberattacks and ensure data integrity.
- Embrace the Data Revolution: Leverage the wealth of data flowing through. Use it to develop innovative features, optimize vehicle performance, and deliver personalized driving experiences.
What Sets A CAN Bus Maker Apart?
Here's a breakdown of benefits that could differentiate the choice of one partner from another.
- Accelerated Life Testers
Testing millions of cycles quickly allows for the provision of robust data on an encoder’s lifespan. Efficiency and reliability of testing procedures are key. - Full Rotation Cycle Definition
Accurately reflects real-world usage, capturing all potential wear and tear points. Realism and thoroughness of testing, compared to less representative cycles, matters. - Vibration Testing
Assures encoders function flawlessly under stress, increasing safety and reliability in applications like off-road vehicles. Durability and performance in harsh environments is critical. - Front and Side-Impact Testing
Simulates potential impacts encoders might encounter in various applications, minimizing failure risk. Look for a proactive value-add approach to safety that takes testing beyond standard requirements. - Abrasion Testing
Evaluates actuator resilience against wear and tear, leading to smoother operation and extended lifespan. Underscore the need for attention to detail and meticulousness in ensuring encoder quality.
Bonus Tips: The right go-to provider of durable, reliable, and thoroughly tested encoder solutions for various demanding applications should stick to effectively prioritizing your needs and demonstrating an unwillingness to sacrifice quality.
Used in specific industries or applications, like autonomous vehicles, medical devices, or aerospace — to name a few — to troubleshooting and diagnostics and best practices and future technologies, the economic impact of the CAN bus is clear: specialists and engineers remain in very high demand.
The CAN Bus Symphony: A Legacy that Endures
The future of the CAN bus is a concerto of evolution and adaptation. It's not about dethroning the king, but about creating a harmonious collaboration where every technology plays its part. By embracing the changing landscape, investing in expertise, and prioritizing security and data utilization, automakers can not only navigate the future of the CAN bus but also leverage its potential to build safer, smarter, and more connected vehicles.
Think of all the new systems and driver-assistance technologies coming online. In the big scheme, this symphony may evolve, but its melody of efficiency and reliability will continue to resonate for years to come, ensuring the smooth ride of the vehicle industry on the road to the future.
Prioritizing Exceptional Service and Solutions
In the competitive arena of solutions providers, a robust technical offering is only half the equation. What truly sets you apart is an unwavering commitment to exceptional customer service.
A well-maintained engine performs well, and a successful provider thrives by focusing on customers. So, how can you locate a partner that prioritizes phenomenal customer service and helps solidify your position?
Building a Customer-Centric Culture Matters
- Invests in Training: Equips teams with the knowledge and tools to handle inquiries effectively. Product training, communication skills, etc.
- Empowered Teams: Autonomy to resolve issues quickly and efficiently. Trusted expertise and culture of accountability.
- Transparency and Clear Communication: Keep customers informed throughout the process. Use clear and concise language, and proactively address potential concerns.
- Accessibility and Availability: Ensure convenient service hours and responsive communication. After the sale service and support and going the extra mile during critical project phases.
Beyond Service: The Extra Mile
- Technical Expertise and Troubleshooting: Profound technical knowledge and problem-solving skills. Goes beyond basic support and provides thorough troubleshooting assistance.
- Customization and Adaptability: Tailors approach to each customer's specific needs and challenges. Offer customized solutions and demonstrate flexibility to accommodate unique requirements.
- Proactive Management: Builds strong relationships, anticipates needs, and offers proactive support and guidance.
Prioritizing exceptional customer service helps foster trust, build lasting relationships, and solidify a position - as a reliable provider of CAN bus system solutions. Businesses thrive on the foundation of unwavering support and genuine care.
The Enduring Symphony
The Controller Area Network (CAN bus) has been the silent workhorse of the automotive vehicle industry for decades, its robust communication orchestrating the complex dance of vehicle functions.
But as technology gallops forward, the future of this technology isn't a solo performance, but a collaborative concerto filled with both challenges and exhilarating possibilities.
At the crossroads of evolution, it will continually adapt. Its strengths – simplicity, reliability, and familiarity – will find continued use in core vehicle communication.
Conclusion: Future of Collaboration and Innovation
The CAN bus system faces a future of evolution and collaboration:
- Newer protocols will complement a more layered network architecture.
- Key trends shaping the future include security, software-defined networks, cloud integration, and interoperability.
- Vehicle makers can embrace flexibility, expertise, and data utilization to thrive.
- The symphony will continue to play a vital role in the future of vehicle technology.
Learn more about Grayhill and our approach to CAN bus system solutions.